Мини-предприятие по производству костных имплантов откроют в Томском госуниверситете
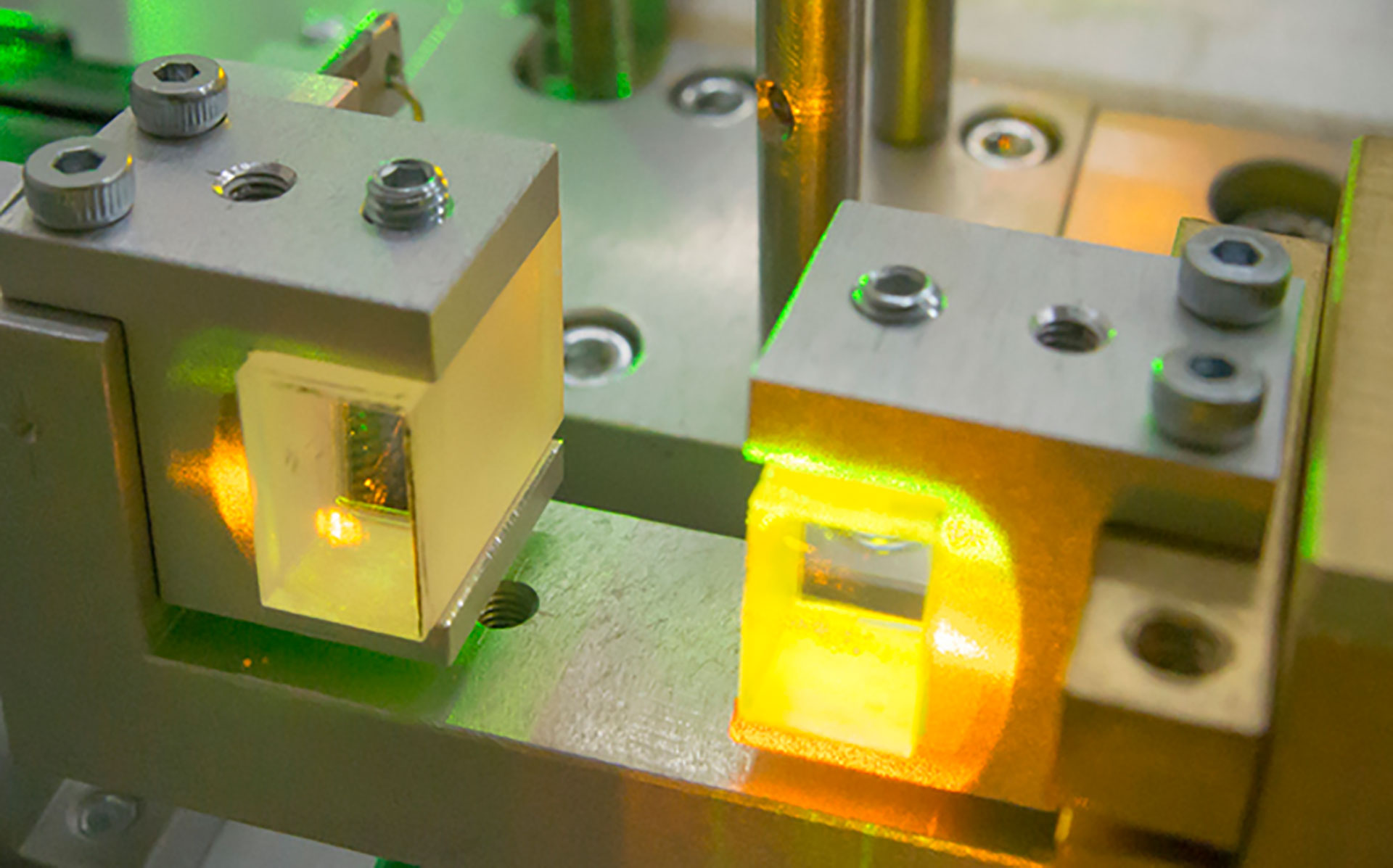
Томский госуниверситете откроет мини-предприятие по выпуску медицинских имплантатов из никелида титана с помощью аддитивных технологий (3D-печать), сообщает сайт вуза. Производство организовано при грантовой поддержке по программе «Студенческий стартап» федерального проекта «Платформа университетского технологического предпринимательства».
На площадке, созданной молодыми учеными, имплантаты будут изготавливаться двумя способами: селективного лазерного спекания (СЛС) и прямого лазерного выращивания (ПЛВ). Для этого в лаборатории сверхэластичных биоинтерфейсов ТГУ были разработаны разные составы для подбора медицинских сплавов. Там также была создана база для производства имплантатов, которые используются для закрытия дефектов костной ткани. Новый проект позволит разработчикам перейти к следующему этапу — 3D-печати продукции. Исследователи будут сравнивать продукцию, изготовленную по методу селективного лазерного спекания и прямого лазерного выращивания в практических условиях. Первый метод достаточно давно используется для создания трехмерных моделей медицинского назначения, в то время как ПЛВ пока применяется в авиации, энергетике и автомобилестроении.
У метода прямого лазерного выращивания есть явные преимущества перед существующими способами производства:
- С помощью ПЛВ можно изготавливать сложные геометрические формы, которые трудно или даже невозможно получить при стандартных методах производства, таких как фрезерование или токарная обработка.
- Метод ПЛВ дает лучшие механические свойства деталей и уменьшает их вес.
- При аддитивном производстве меньше отходов, поскольку используется только нужное для создания конструкции количество материала.
Александр Гарин, руководитель проекта, сотрудник лаборатории сверхэластичных биоинтерфейсов ТГУ, рассказал, что ученые проведут сравнение свойств, функциональности и биосовместимости протезов, изготовленных разными способами. «Проект позволит достичь максимального соответствия механическим и химическим параметрам организма пациента. В результате получаемые имплантаты будут учитывать потребности каждого медицинского случая и отвечать всем требованиям безопасности, эффективности и удобства использования, что улучшит качество жизни пациентов», — пояснил он.
Что особенно важно, по мнению разработчиков, что в реконструкции кости в России нуждаются десятки тысяч пациентов, а инновационные подходы делают этот вид медицинской помощи более оперативным и персонализированным.
«ФармМедПром» также рассказывал, что ученые Курчатовского института и РНЦХ им. Петровского с помощью 3D-печати изготовили первые биоразлагаемые спинальные кейджи — конструкции для воссоздания поврежденного межпозвонкового диска и соединения поврежденных позвонков.