Шесть скрытых несоответствий, из-за которых фармпроизводства теряют до 50% рабочего времени
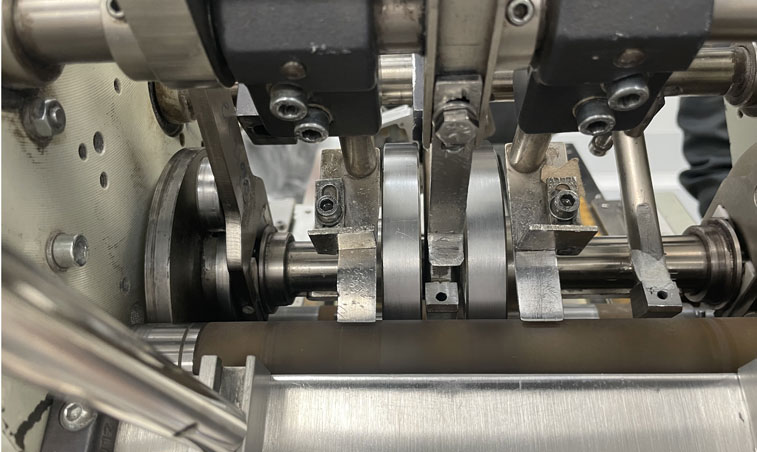
Любая фармацевтическая компания сталкивается с простоями производственных линий. Чаще всего они происходят из-за сбоев оборудования, а поиск причин и их устранение может занимать 30–50% рабочего времени. В итоге процесс останавливается, выпуск лекарственных препаратов замедляется, а каждая пауза – это потерянные деньги.
Чтобы сократить время простоя, важно, чтобы производственный персонал обладал соответствующими знаниями и навыками. Для этого Сервисная служба АО «Промис» во главе с Олегом Самсоновым создала специальную 8-часовую программу подготовки наладчиков, которая включает теоретический и практический блоки.
Во время проведения практического занятия на одном из фармпроизводств сервисные специалисты компании «Промис» выявили сразу шесть критических несоответствий на картонажной линии. Каждое из них провоцировало регулярные сбои и затягивало процесс производства продукции. Проблемы были связаны и с качеством материала, и с техническим состоянием оборудования:
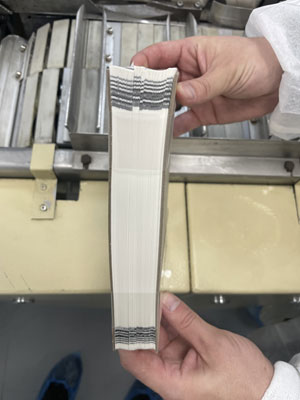
- Ненадежная упаковка инструкции. Один из поставщиков оборачивал пачки с инструкциями термоусадочной пленкой, но фиксировал их бандерольной лентой только по центру. Другой – вообще не использовал термоусадочную пленку, скрепляя инструкции лентами с двух сторон по углам. В результате партии поступали на производство уже с повреждениями, что приводило к замятию листов-вкладышей и постоянным остановкам оборудования.
- Несоответствие габаритов инструкции. Размеры листов в одной пачке имели расхождение до 3 мм при допуске ± 1 мм. В результате производственная линия останавливалась, если инструкция отличалась от требуемых размеров.
- Неправильное направление долевых волокон у инструкции. Это не только провоцировало сбои в работе оборудования, но и приводило к браку, потерям листов-вкладышей и увеличению технологических отходов.
- Некорректная работа электромагнитного клапана. Система включалась вовремя, но выключалась раньше положенного, из-за чего забор листов был нестабильным. После замены электромагнитного клапана на механический оборудование стало работать исправно.
- Износ механической части удерживающего язычка. Механизм не мог отделять нижние листы от стопы и передавать их поштучно. Для стабильной работы потребовалась замена детали.
- Ошибка в установке кулисного камня на фальцевальном валу. Деталь была установлена в перевернутом виде, что затрудняло настройку валов и ухудшало качество фальцовки.
Эти проблемы, на устранение которых сотрудники тратили до половины своего рабочего времени, стали очевидными после прохождения авторского курса Олега Самсонова.
«Как правило, большая часть простоев оборудования вызвана недостаточной квалификацией кадров. У персонала иногда не хватает теоретических знаний и практических навыков для понимания причин сбоев. Наша цель – помочь разобраться в нюансах, чтобы добиться стабильной работы оборудования», — отметил руководитель Сервисной службы АО «Промис» Олег Самсонов.
«Наши сотрудники научились выявлять типовые несоответствия на упаковочной линии и оперативно их устранять, а значит сокращать время простоев и экономить деньги. Раньше мастеров для наладки оборудования могли ждать неделю и даже больше, сейчас справляемся сами всего за несколько часов», — поделился представитель отдела главного технолога фармацевтической компании.
Дополнительный плюс курса – возможность получить экспертные рекомендации по устранению недочетов прямо на производственной линии во время практических занятий. Это помогает оперативно стабилизировать работу оборудования и в разы сократить количество сбоев.
Получить демоверсию курса Сервисной службы АО «Промис»
Реклама АО «Промис»
Erid: 2SDnjc5ih4q